Welcome to FiberCell Laboratories: Your Bioproduction Partner in Biology
At FiberCell Laboratories, we specialize in contract manufacturing of cell-derived products, offering innovative solutions to scale up cell culture and enhance bioproduction efficiency. With over 20 years of expertise in hollow fiber bioreactor technology, we provide researchers and organizations with unparalleled productivity—achieving up to 100X greater output compared to traditional flask culture methods.
Why Choose FiberCell Laboratories?
Hollow Fiber Bioreactor Advantages
Our hollow fiber bioreactors are designed to revolutionize cell culture with:
- High Concentration: Secreted products are concentrated up to 100X.
- Uniform Modifications: Achieve complete and consistent post-translational modifications.
- Purity and Efficiency: Significant reduction in contaminating DNA and intracellular proteins.
- Adaptability: Easy transition to protein-free, chemically defined, animal component-free cGMP serum replacements.
- FDA Compliance: Utilize CDM-HD, our cGMP-compliant serum replacement for regulatory-grade production.
Explore more about our hollow fiber advantages to elevate your bioproduction processes.

Our Expertise in Contract Manufacturing
FiberCell Laboratories offers a comprehensive range of contract services tailored to meet your bioproduction needs:
- Monoclonal Antibody Production
Streamline antibody generation with high-yield, scalable production systems. - Recombinant Protein Production
Produce large quantities of high-quality recombinant proteins efficiently. - Exosome Production
Optimize exosome yields with precise and clean cell culture methods. - Conditioned Medium
Generate cell-specific growth environments for advanced research applications. - Virus and Vaccine Production
Scale up virus and vaccine production for research and therapeutic needs. - Growth Factor Production
Efficiently produce critical growth factors with uniform quality and consistency.
Learn how our contract manufacturing services can help advance your research and development.
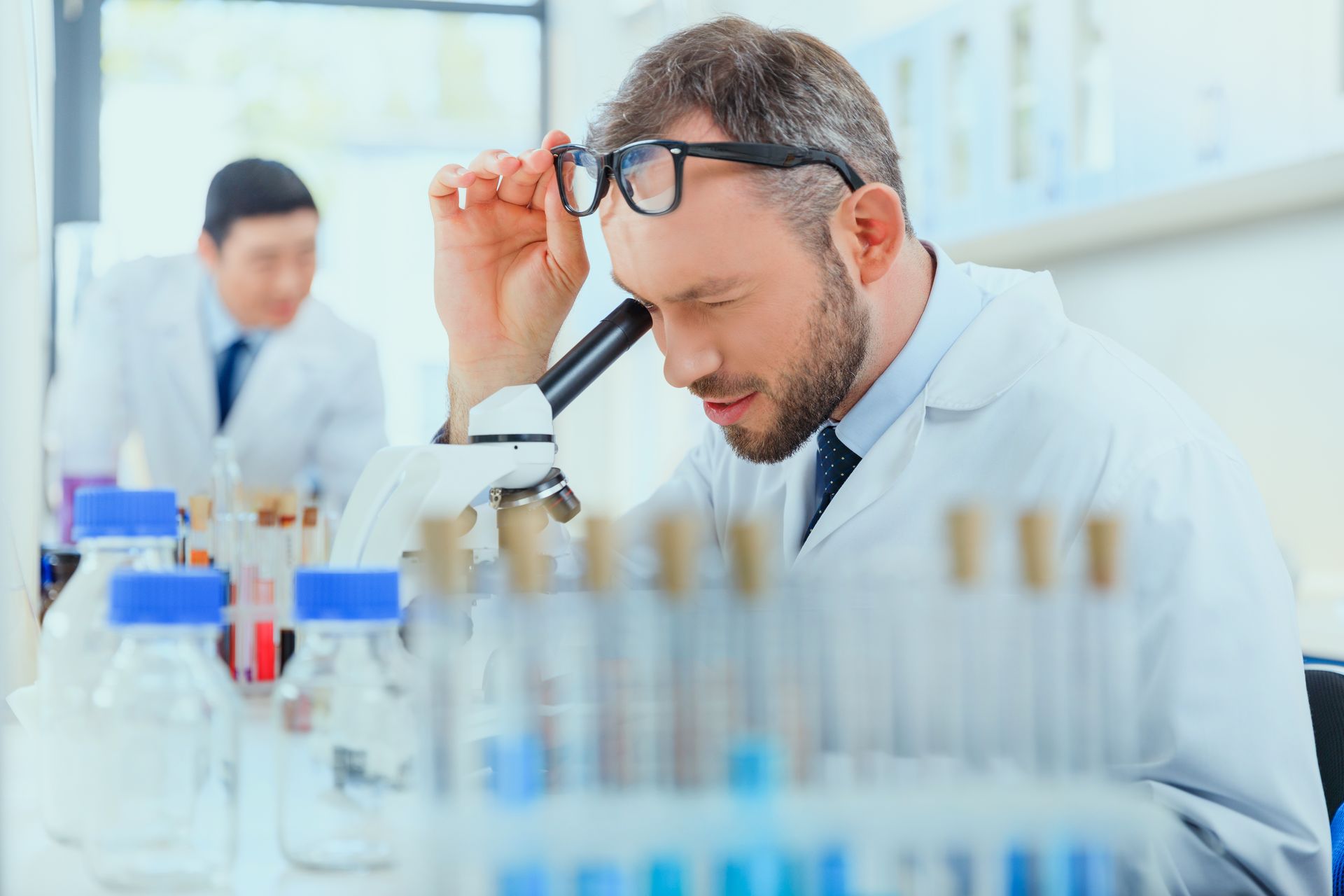
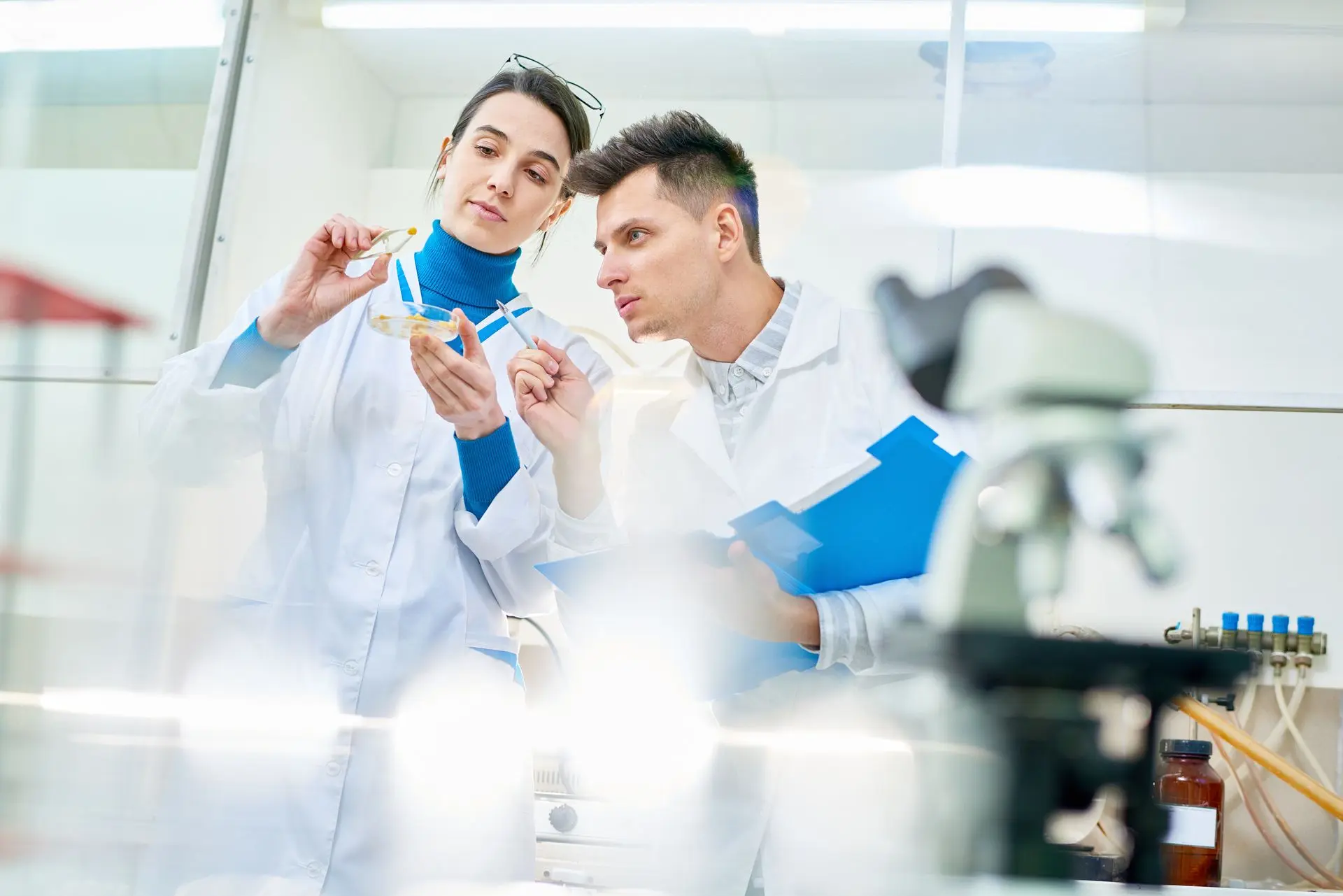
Our Commitment to Quality and Compliance
At FiberCell Laboratories, we prioritize delivering products and services that meet the highest industry standards:
- FDA Compliance: Our cGMP serum replacements ensure safe and regulatory-compliant bioproduction.
- Chemically Defined Media: CDM-HD eliminates animal components, ensuring contamination-free production.
- Long-Term Productivity: Continuous production over several months can yield gram quantities of proteins and antibodies.
Discover the benefits of FDA-compliant bioproduction solutions with FiberCell Laboratories.
How We Can Support Your Research
Scalable Solutions: Transition from flask cultures to hollow fiber bioreactors seamlessly.Enhanced Productivity: Achieve higher yields and purity for your cell-derived products.Expert Guidance: Leverage over two decades of expertise in hollow fiber technology.Request a consultation to learn how we can optimize your bioproduction.
Get Started with FiberCell Laboratories
Partner with FiberCell Laboratories to harness the full potential of hollow fiber bioreactor technology. From monoclonal antibodies to vaccines, our tailored solutions drive innovation and productivity in biological research and production.
Elevate your bioproduction with FiberCell Laboratories—where innovation meets productivity.
Recombinant Protein Production
The production of recombinant proteins and conditioned medium from mammalian cells can be such a cumbersome process that for many laboratories the use of mammalian expression systems is to be avoided. Large numbers of plates, flasks or roller bottles are required or the use of a stirred tank vessel is mandated. The cell culture conditions provided by these methods are inherently non-physiologic. Hollow fiber bioreactors provide a tremendous amount of surface area for cell attachment and the high cell density permits the use of our CDM-HD serum replacement and can also result in improved protein folding and more uniform post-translation modifications. Protein concentrations are in the range of 100 ug to 300 ug/mL/day and the production of 10’s of mg on up to gram quantities of proteins is possible. The protein of interest becomes a significant component of the harvested supernatant and the small volumes facilitate purifications.
Secreted proteins can be 100 times more concentrated vs. tissue culture supernatant.
- Reduced serum requirements facilitates purification
- Small harvest volume for easy handling
- No splitting of cells required, cartridge maintenance just 15 minutes a day
- Cultures can be maintained for several months of production
- Optimal cell culture conditions can result in improved protein assembly and folding
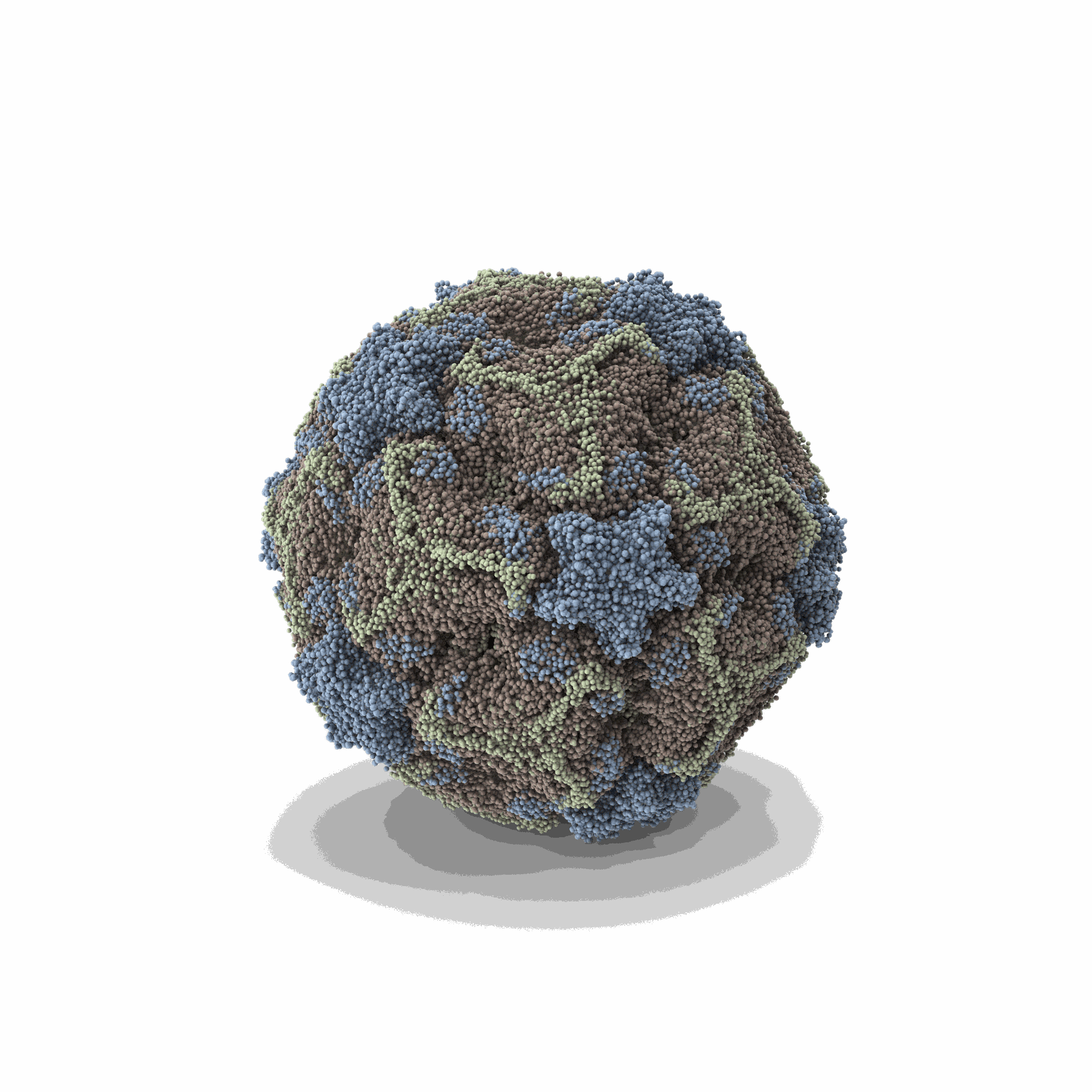
Monoclonal Antibody Production
A hollow fiber bioreactor from FiberCell® Systems is the ideal method for the in vitro production of 25mg on up to gram quantities of a monoclonal antibody. A technologically advanced high-gross-filtration rate hydrophilic polysulfone fiber with a molecular weight cut off (MWCO) of 20kd is specified. Hybridomas secrete an inhibitory factor called TGF-Beta that in its active form has a molecular weight of 27kd. The MWCO of the hollow fibers permits this inhibitory cytokine to diffuse away while the secreted antibody and cells remain in the small volume of the extra-capillary space. The gross filtration rate of the polysulfone fiber is 10X higher than that of cellulosic fibers for more rapid exchange of nutrients and waste products. Cell densities of 108 or higher are attained facilitating the reduction of serum, the adaptation to commercially available serum free formulations and the use of FiberCell® Systems’ CDM-HD.
CDM-HD is a chemically defined, protein free, animal component free CGMP compliant serum replacement optimized for hollow fiber and designed to take advantage of the unique cell culture conditions found within a hollow fiber bioreactor. Harvest volume is 20-40 mL and antibody concentration can range from .5 mg/mL to 5 mg/mL. Since no animal host is required (such as mice or nude mice), chimeric (mouse/human) and non-murine antibodies such as rabbit, rat and hamster can be easily produced. We have demonstrated a reduction in apoptosis when cells are cultured in hollow fiber bioreactors. When used with CDM-HD, contaminants such as lipids, endotoxin, proteins, intracellular DNA and viruses are reduced or eliminated. This lack of contaminants can simplify or reduce the purifications steps required improving overall yields as well.
The scale-up of antibody production has just been made easier. The C5011 cartridge can be managed in the same manner as the C2011 but with 2X greater productivity and twice the antibody concentration. The C5011 is the same cartridge as the C2011 but with more than twice the oxygenation capacity.
Data shared by a FiberCell customer: | |
Catridge | C5011 |
Cell Line | SP2 Hybridoma |
Medium | H-SFM |
Medium Consumed Per Day | 1 Liter |
Total Medium Consumed | 66 Liters (11 weeks production) |
Total Antibody Produced | 1.7 grams after purification |
Total Harvest Volume | 450 mL |
Average Concentration (after purification) | 3.77 mg/mL |
Production of multiple gram amounts of a monoclonal antibody can be easily attained using the C5011 cartridge.
To demonstrate the utility of CDM-HD, a direct comparison was performed between monoclonal antibody production from the same standard murine SP2 clone in a 20 liter wave bag containing 10 liters of medium, T175 tissue culture flasks (1.2 liters consumed, data normalized to 10 liters for comparison) and a FiberCell® Systems C2011 medium 20 kd MWCO hollow fiber bioreactor cartridge, set up according to the manufacturer’s protocol and allowed to consume 10 liters of medium. Flask data and Wave bag data were generated using a commercially available serum free hybridoma medium (SFM), while FiberCell® Systems data was generated using DMEM medium with 10% CDM-HD chemically defined serum replacement. Total protein was measured before and after Protein A purification and antibody quantitation performed on column eluent.
Figure one: Purified antibody and ratio of antibody to total protein for the three systems. Flask culture yielded almost as much antibody as the FiberCell® Systems cartridge, however the antibody in the FiberCell® Systems harvests is about 50X more concentrated. Note the large amount of extra protein from the wave bag, probably due to cell lysis. Non-antibody protein in the flask is from the serum free media, which is not protein free. FiberCell® Systems culture when used with CDM-HD is free from exogenous protein and cell lysis.
Figure two: Antibody yield per 10 liters of medium consumed, total harvested antibody concentration prior to purification. Note the extremely high concentration of antibody in the FiberCell® Systems hollow fiber bioreactor cartridge. 200 ml of harvested supernatant was equivalent to 10 liters of culture supernatant from the other systems again reflecting the 50 X higher concentration of antibody generated in the FiberCell® Systems bioreactor cartridge.
These data represents a direct comparison between a Wave bioreactor bag, standard T175 tissue culture flasks and a medium sized FiberCell® Systems C2011 hollow fiber bioreactor cartridge. The FiberCell® Systems cartridge produced 6 times the amount of antibody than the Wave bag produced at 50 times higher concentration with no exogenous protein. The FiberCell® Systems cartridge produced slightly more antibody than the T175 flasks but at a concentration 50X higher with no detectable exogenous protein. CDM-HD is optimized for higher density cell culture, and therefore the media employed in this comparison were not identical. The comparison demonstrates the power of the combination of hollow fiber bioreactors and a medium designed to take advantage of this higher cell density. It should also be noted that the Wave bag is a 1-2 week batch mode process, while the FiberCell® Systems cartridge can be maintained producing antibody for more than 6 months if so desired, further increasing amount of antibody produced per reactor cycle or annum.
Above: RAb M5114 Production results from the Fibercell Hollow Fiber System. Cartridge used was the C2011 20 kd MWCO polysulfone fiber and medium used was DMEM with 10% CDM-HD. Protocol followed was per the FiberCell Systems manual. The M5/114.15.2 monoclonal antibody reacts with the mouse major histocompatibility complex class II, both I-A and I-E subregion encoded glycoproteins. In the gel shown, purified M5114 was a positive control purified from Protein G column, lane 1. Lanes 2,3, and 4 are harvests from the cartridge on day 7, 9 and 12. No purification has been performed. Note how clean the harvests are and free from extraneous proteins. Lane 5 is 10X concentrated supernatant from a T-flask using DMEM and 10% CDM-HD. Lane 6 is from a T flask using DMEM and 10% serum. 3 ug of control was loaded, and the supernatant from HFB was loaded with 2ul of each. The supernatant from T-flasks were 10x concentrated and i loaded 2 ul of each. Based on the gel, it is estimated that the concentration of supernatant from HFB was about 2.5 mg/ml. 140 ml of supernatant was harvested to date for a total about 350 mg of non-purified antibody. Both SDS-PAGE gel and gel filtration analysis showed that the antibody from the hollow fiber bioreactor was very clean and properly folded. The cartridge was allowed to run for several weeks after this initial data was collected, producing additional antibody. Data courtesy of Liying Lu, University of Massachusetts, Worcester, Worcester, Massachusetts.